Just when you thought it was safe to buy that new machine for your production line…
I thought long and hard about an original analogy that WASN’T the cliched iceberg, so I’ve come up with a shark instead. Both are pretty scary from above the surface, but it’s what’s beneath the water that will send shivers down your spine.
Welcome to the world of capex machinery procurement.
This blog is for Engineering, Manufacturing and Procurement professionals alike. My aim is to make you aware of some of the myriad costs that feature within capex machinery procurement that won’t necessarily be identified on a supplier quotation, but definitely DO need to be considered in your sourcing evaluation.
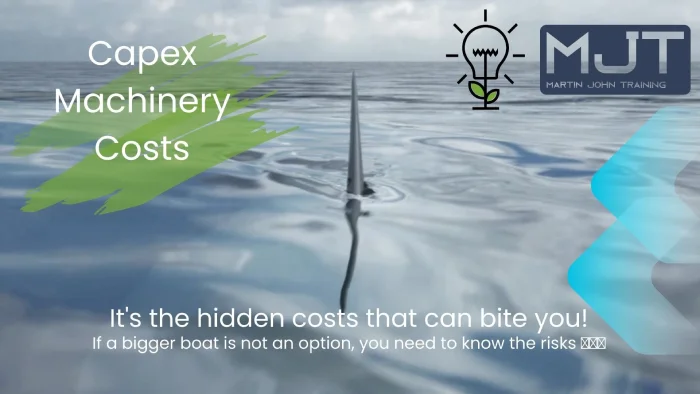
If you’re a Procurement professional who’s new to the category and don’t have an engineering or production background, entering into the realm of buying Capex can be just like swimming in shark-infested waters without so much as a robust pair of Speedos to protect you.
It’s a heavily technical area, dominated by impenetrable jargon, with sourcing often led by the technical teams and sadly, Procurement mainly being bystanders trying to shave a few percent off the purchase price after the deal has been agreed. No Procurement professional worth their salt (honestly, I didn’t mean to make a pun there) would be comfortable with this situation.
Fear not though, just like any other category (even IT or Marketing Services) acquiring the knowledge to not only manage the category effectively but to also drive additional value from it (more on that in a future blog) is totally learnable. Blimey, even I have done it.
But in this blog, I’m focusing on highlighting some of the lesser-known costs of which you should be aware.
There really are so many costs to consider, and remember, many of these costs will be incurred throughout the lifetime of the asset – which could be more than 10 years!
If you don’t consider the total cost of ownership (“TCO”) when planning and executing these projects, these costs could sink your project, your budget or even your career! Gulp.
The costs can be put into two broad buckets:
Above-the-line costs (these are the obvious ones and should be on the suppliers’ quotation)
· Purchase price
· Packaging
· Transport
Below-the-line costs (one-off costs and ongoing costs)
· Installation
· Spare parts
· Maintenance
· Energy
· Labour
· Plus, at least 15 more!
While the “above the line” costs are obvious, the “below the line” costs are less so and I’ll explain each of the latter here.
Installation – it’s usually the responsibility of the buyer to arrange installation. In some cases it’s not quite as simple as “plug and play”; existing equipment may need to be physically moved to accommodate the new purchase, so the costs could be substantial. You’ll need to consider both mechanical and electrical installation costs.
Spare parts – This will be an ongoing cost of operating the machine and will need to be provisioned, usually in operational expenditure (“Opex”). Consumption will be directly related to the rate of production. How much will it cost you to buy, store and replenish the inventory of spare parts? Remember, spare parts availability is a critical aspect in ensuring that machine uptime is met.
Maintenance – Similar to spare parts in as much as the costs will be incurred proportionally to production rate. You’ll need to consider the most appropriate maintenance intervals and the scope of each maintenance event over the lifetime of the machine (a bit like an interim and full service with your car).
Energy – Again, energy consumption will be incurred in proportion with production, although the machine may consume power while being idle. Given the current higher cost of energy, this cost is likely to represent a larger proportion of total cost, and if your process requires thermal energy then this could be one area where you’d want to drill down on the suppliers’ specifications to identify any major differences in the rate of energy consumption.
Labour – how many people are required to operate the machine? Different machines may have different crewing requirements so could be a source of cost differentiation. Labour is quite a “sticky” cost, too, as it’s not incurred in a way that’s directly proportional to production. For example, if you’re producing 1,000 units or 10,000 units per day off the same machine, you’ll likely incur the same labour costs.
I’ve just scratched the surface here by way of bringing home the importance of considering TCO for Capex machinery projects.
If you want to find out how to manage and get the best value from the full list of costs you can expect on a capex machinery project, my 1-day machinery procurement training course (which I teach face to face or on-line) will equip you with what you need.
You’ll also learn about the multitude of risks associated with Capex and how to mitigate them to help you meet your project budget and timeline.
Please get in touch with me for details.
The best days lie ahead.
Martin